Correctly Modeling a Make-up/Blow-down Block in ProMax
Craig Spears
July 10, 2012
Correctly Modeling a Make-up/Blow-down Block in ProMax
ProMax utilizes a Make-up/Blow-down block for many open-loop systems to keep the process in an accurate steady-state condition. These processes have losses of the circulating liquid through solubility and/or entrainment, and the losses must be recovered by adding additional solution over time. Utilizing the Make-up/Blow-down block allows ProMax to easily maintain a heat and material balance on the system, and for your circulation rate to be maintained at a desired flow rate without requiring you to calculate any losses in the process yourself. This block may be used in more than one way, and I will show two common methods here: modeling glycol dehydration make-up and modeling amine sweetening make-up.
Using the Make-up/Blow-down Block for Glycol Dehydration
First, the temperature and pressure in the make-up stream are user-defined: typically the process pressure is set and the temperature of the liquid in the storage tank is used. These specifications are required so ProMax can calculate the outlet temperature and pressure of the outlet stream (22 in this example). Since the glycol circulating in the unit is essentially pure glycol, any make-up required in the system will be the purchased purity of glycol, for example 99.9wt% TEG / 0.1% Water. In the following two screenshots, you can see all of the user-set specifications in the blue type. The composition was set on a Mass Percentage basis, and the temperature and pressure were also set. The flow rate is left unspecified by the user.
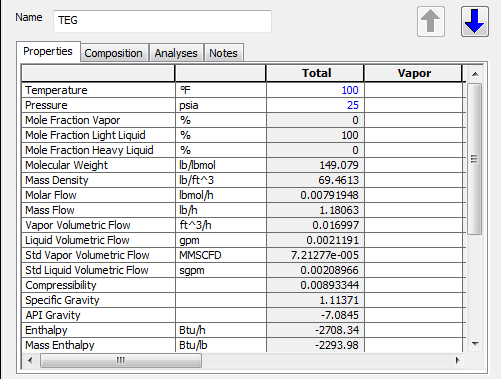
For the glycol case being demonstrated here, you can see in the following screenshot that the “TEG Makeup” block has pulled in the information from the “TEG” stream to set the “Makeup Bulk Composition” column in the block. The gray background shows that this was not user-set in the Make-up/Blow-down block.
The final piece of information is the desired circulation rate for the glycol in the open-loop system. For our example the desired flow rate is 20 sgpm. This value is placed downstream of the Make-up/Blow-down block. Our general recommendation is to set it immediately downstream (stream 22 in this example), but this is not absolutely required. By setting the flow rate downstream, ProMax can then calculate what the required make-up stream flow rate must be to maintain the desired circulation rate. For this example, I can see in the above screen-shot that ProMax has calculated the “TEG” stream flow rate to be 0.0021191 sgpm, which indicates that there was a loss of solution throughout the open-loop system of the same quantity. The losses will be part water and part glycol, but since our goal in the glycol system is to maintain as high purity of glycol as possible, we make-up with the “pure glycol” that we indicated earlier was purchased, or 99.9wt% glycol. The overall purity of the glycol circulating in the system is dependent on the pressure, temperature, and other conditions of the glycol regenerator and operation decisions of the unit.
Using the Make-up/Blow-down Block for Amine Sweetening
The temperature and pressure of the make-up stream are user-defined exactly the same as with the glycol case: typically the process pressure is set and the temperature of the liquid in the storage tank is used. Again, these specifications are required so ProMax can calculate the outlet temperature and pressure of the outlet stream (18 in this example).
The flow rate of the make-up stream is determined in the same method as the glycol example above. The outlet stream, 18 in this example, has a circulation rate set. Again, it is not required to be set in the stream directly downstream of the Make-up/Blow-down block, but it is our general recommendation. ProMax will compare the desired flow rate set in this outlet stream with the flow rate of the stream that is feeding into the Make-up/Blow-down block and determine whether material must be added or removed (or both in some cases) from the system.
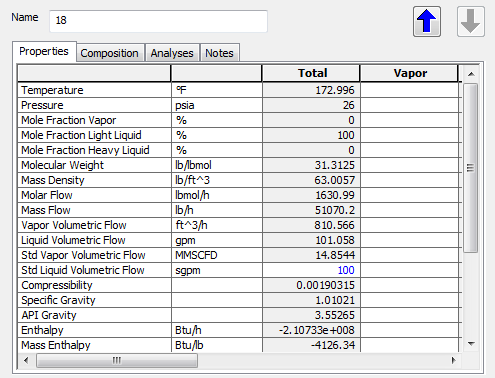
However, unlike the glycol case, a make-up stream composition is not directly set by the user. You can see in the following screenshot that the make-up stream composition has a gray background, indicating that it was not set by the user, and instead was calculated by ProMax. The amine that circulates in this system is not pure amine, and is instead a solution of amine mixed with water. Since there will be a different percentage of water loss versus amine loss in the system compared to the circulating solution strength, the make-up stream concentration cannot be predetermined.
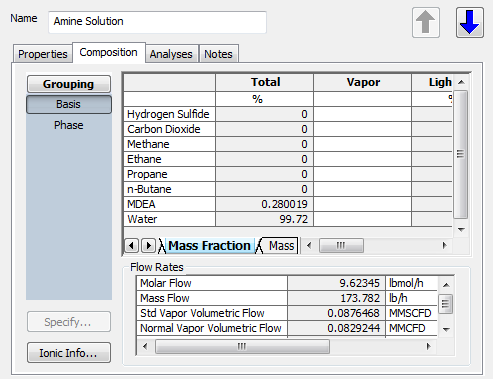
Instead, the Make-up/Blow-down block provides a method of allowing it to calculate the amount of amine and water to add through the make-up stream separately. The “Target Outlet Composition” column allows you to specify an exact value that you would like maintained in the outlet stream. In the current example, the MDEA is specified to be exactly 50% Mass Fraction in the outlet stream, 18. If you have an activated amine system, or a mixed amine system, then typically all desired concentrations of amines and activators are set in the “Target Outlet Composition” column (e.g. 45% MDEA, 2% Piperazine). The “Makeup Bulk Composition” column allows you to determine what other components will be added to the make-up stream, if required, to maintain the desired flow rate, as set in stream 18. In the case of an amine sweetening unit, this is almost always 100% water.
Note: this is not stating that the make-up stream will be 100% water; the amount of any component in the left-hand column will be added as well so that the final solution of the outlet stream matches both the “Target Outlet Compositions” set and the overall stream flow rate.
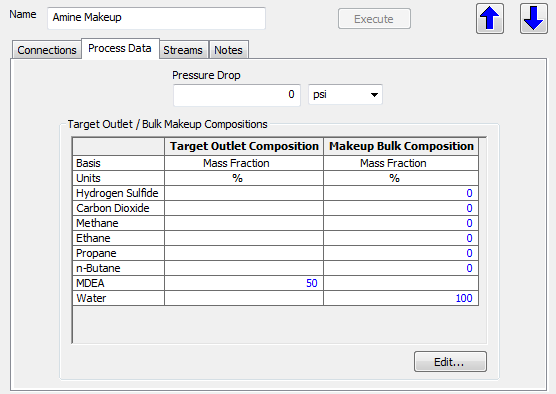
A few additional notes:
- All streams must be attached, even if there is anticipated to be either no make-up or blow-down in the system
- Typically for these applications the Make-up/Blow-down block should be placed in the lean solvent stream
- ProMax cannot execute upstream through the Make-up/Blow-down block (it will not back-calculate)
- When specifying “Target Outlet Composition”, the values entered cannot add to unity (100%) because it would not be possible to achieve the required make-up to satisfy the specification
- When specifying “Makeup Bulk Composition”, the values entered must add up to unity (100%)
- For cases where the make-up is an oil with multiple components (e.g. lean oil absorption units), the oil should be entered directly in the make-up stream to avoid entering individual oil cuts separately in their relative amounts in the make-up specification dialog.
- The make-up stream flow rate cannot be specified since it is always a calculated value